Epoxy Powder Coating for Electrical Insulation
Epoxy powder coatings are ideal for insulating electrical components due to their high dielectric strength and interlocking molecular structure.
These coatings are highly effective at preventing high voltage breakthrough, making them a preferred choice for electrical insulation applications.
215 Tyburn Road, Erdington, Birmingham B24 8NB
(800 Yards from Junction 6 M6 Spaghetti Junction)
Powder Coatings Ltd – Established over 50 years. ISO 9001 Approved Quality Systems.
All you need to know about Epoxy Powder Coating and Electrical Insulation
What Is Dielectric Strength and Why Is It Important?
Due to their tight and interlocking molecular structure, epoxy powder coatings exhibit excellent dielectric strength, making them a great solution for insulating electrical components to prevent high-voltage breakthrough.
A 100-micron coating of epoxy powder has a dielectric strength in the region of 3000 volts. This means that a voltage of over 3000 volts can be applied to the surface of the coating without any breakthrough to the underlying substrate. The dielectric strength can vary depending on the specific formulation of the epoxy powder.
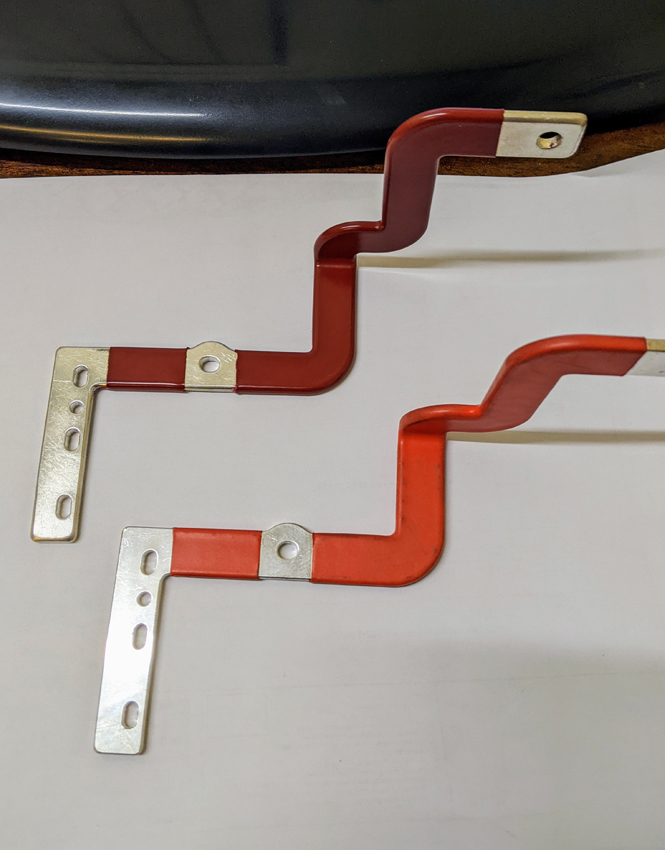
Units of Measurement for Dielectric Strength
Dielectric strength is often specified using different units of measurement, which can be confusing. Common units include:
-
Volts per mil: A mil is 0.001 of an inch (25.4 microns).
-
KV/mm: Where KV represents kilovolts (1,000 volts), and a micron is one-thousandth of a millimetre.
Understanding these units is crucial when determining the required dielectric strength for specific components and applications.
Applications of Epoxy Powder Coating in Electrical Insulation
Epoxy powder coatings can be applied to a wide variety of electrical components, including:
-
Bus Bars for electrical connections
-
Electric Motors and associated parts
-
Transformers and electrical switchgear components
These coatings provide effective insulation for components that are exposed to high voltages and are critical in ensuring the safety and functionality of electrical systems.
Epoxy Powder Coating Application Methods
There are two primary methods for applying epoxy powder coatings to electrical components: electrostatic spraying and the fluidised bed method.
Electrostatic Spraying
Electrostatic spraying is the most common method for applying epoxy powder coatings to electrical components. This technique is ideal for larger batches of parts and offers precise control over coating thickness. Multiple layers can be applied to achieve the required dielectric strength. This method is widely used in the industry for both high-volume production and precision coating.
Fluidised Bed Method
For applications that require thicker coatings for high-voltage breakthrough resistance, the fluidised bed method is used. In this process, parts are pre-heated and dipped into a bed of epoxy powder that is aerated with compressed air. The powder fuses immediately because of the heat, curing as it is applied. This method is ideal for achieving thicker coatings (200-500 microns).
Potential Technical Issues with Epoxy Powder Coating
While epoxy powder coatings are highly effective, there are some technical issues that need to be addressed during the coating process:
-
Flow Issues at Sharp Edges: Epoxy powder coatings can sometimes flow away from sharp edges, causing thinner areas at these points. This may result in electrical breakthrough when the component is tested. It’s important to consider these areas during design and coating thickness specification to avoid potential failures.
-
Connection Points: The connection points of a component usually need to be free from epoxy powder coating. This is typically achieved through masking with high-temperature masking tape or pre-made masks. Custom masks can be designed and applied to ensure that no coating is applied to specific areas.
-
Substrate Adhesion: The substrate material of the component can influence the adhesion of the epoxy coating. Tin plating is a popular choice but can cause adhesion problems due to its low coefficient of friction. Silver or electroless nickel plating are often preferred for better adhesion.
Why Choose Epoxy Powder Coating for Electrical Insulation?
Epoxy powder coatings offer a highly effective and durable solution for electrical insulation needs. Their high dielectric strength, chemical resistance, and durability make them ideal for use in electrical components exposed to high voltages. Whether you need to coat electric motors, transformers, or bus bars, epoxy powder coating provides reliable insulation to prevent electrical breakthroughs and ensure component safety.
Expert Epoxy Powder Coating Services
We specialise in the application of epoxy powder coatings for electrical insulation and offer expert advice on both new and existing projects. Our team ensures that your electrical components meet the required dielectric strength specifications, providing reliable protection against high voltage breakthrough.
Contact us today to learn more about our epoxy powder coating services and how we can help with your electrical insulation needs.
Established over 50 years — Central location, Junction 6 M6 Spaghetti — ISO 9001 Approved quality systems - Established over 50 years — Central location, Junction 6 M6 Spaghetti - ISO 9001 Approved quality systems — Established over 50 years - Central location, Junction 6 M6 Spaghetti — Established over 50 years - Central location, Junction 6 M6 Spaghetti — ISO 9001 Approved quality systems - Established over 50 years — Central location, Junction 6 M6 Spaghetti - ISO 9001 Approved quality systems — Established over 50 years - Central location, Junction 6 M6 Spaghetti — ISO 9001 Approved quality systems - Established over 50 years — Central location, Junction 6 M6 Spaghetti - ISO 9001 Approved quality systems — Established over 50 years - Central location, Junction 6 M6 Spaghetti — ISO 9001 Approved quality systems - Established over 50 years — Central location, Junction 6 M6 Spaghetti - ISO 9001 Approved quality systems — Established over 50 years - Central location, Junction 6 M6 Spaghetti — ISO 9001 Approved quality systems - Established over 50 years — Central location, Junction 6 M6 Spaghetti - ISO 9001 Approved quality systems — Established over 50 years - Central location, Junction 6 M6 Spaghetti — ISO 9001 Approved quality systems - Established over 50 years — Central location, Junction 6 M6 Spaghetti - ISO 9001 Approved quality systems — Established over 50 years - Central location, Junction 6 M6 Spaghetti — ISO 9001 Approved quality systems - Established over 50 years — Central location, Junction 6 M6 Spaghetti - ISO 9001 Approved quality systems — Established over 50 years - Central location, Junction 6 M6 Spaghetti — ISO 9001 Approved quality systems - Established over 50 years
Address
215 Tyburn Road, Erdington,
B'ham B24 8NB See Location
Hours
Mon to Thurs 7am till 4pm
Fri 7am till Midday
Email & Web
roger@powder-coatings.co.uk
www.powder-coatings.co.uk